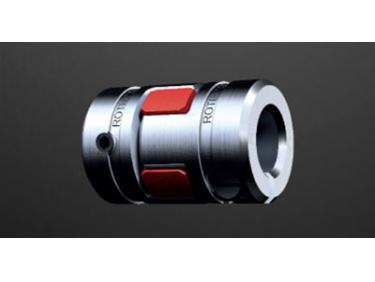
ROTEX® GS Backlash-free
Product characteristics
• Backlash-free shaft connection under prestress
• Small dimensions - low flywheel mass
• Maintenance free, easy to check visually
• Various kinds of elastomer hardness of spiders
• Finish bore according to ISO fit H7 (except for clamping hub),
feathter key optionally available from Ø 6 mm according to DIN 6885 sheet 1 - JS9
• Ex Approved according to EC Standard 94/9/EC (without feather key according to category 3)
Coupling description
ROTEX® GS is a three-part, axial plug-in coupling backlash-free under pre-stress. In spite of its vibration-damping
characteristics it is torsionally stiff so that it is not necessary to make any concessions to accuracy even with
highly dynamic servo drives. ROTEX® GS is available in different types of hubs which can be combined within one coupling
size.
Additional Information
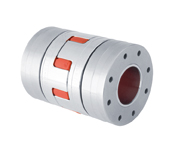
positioning by the drives is necessary. The different hub types and kinds of
Shore hardness provide for the optimum coupling for every application in
automation. It is considered to be the standard solution for ball screws
with an incline of s<40. In servo hydraulics our ROTEX® GS is used more and
more frequently, too.
Please observe the selection advice in our company catalogue. Our
applications consultants will be pleased to assist you with the selection of
the coupling.
Operating Principle
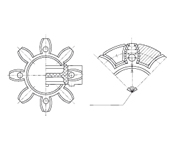
assembly". The pegs arranged reciprocally on the spider prevent the spider
from touching the hub over the entire surface. Observing the distance
dimension E ensures the ability of the coupling to compensate
for displacements. The plug-in force varies depending on the Shore hardness
and prestress of the spider (see comments in the mounting instructions KTR-N 45510).
By observing the gap dimension "s" the electrical isolation is ensured, as well as
a high service life of the coupling. This fact is gaining more and
more importance, due to the increasing precision of shaft encoders and the
existing demand for electro-magnetic compatibility.